The Transformative Power of Liquid Silicone Injection Molding Machines
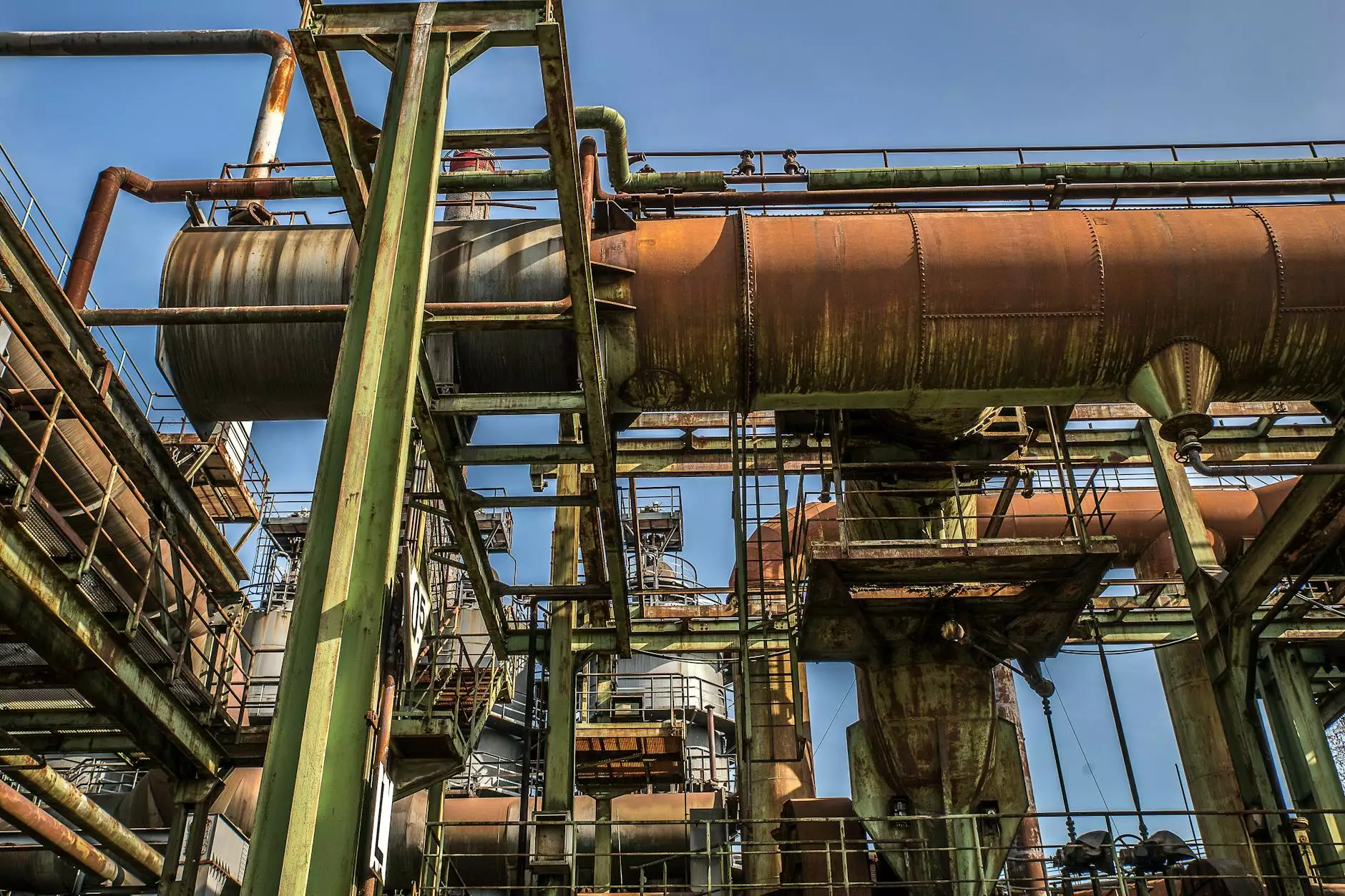
The evolution of manufacturing processes has significantly impacted various industries. Among the latest advancements, Liquid Silicone Injection Molding Machines have emerged as vital tools, especially in the fields of electronics and medical supplies. These machines offer an unparalleled approach to creating complex, high-performance products with remarkable durability and flexibility. In this article, we will delve into the intricacies of these machines, their benefits, applications, and their role in reshaping modern production methodologies.
Understanding Liquid Silicone Injection Molding
Liquid silicone injection molding is a specialized manufacturing process that utilizes liquid silicone rubber (LSR). This process is characterized by its ability to create intricate designs with a high level of precision. LSR is a thermoplastic, which means it can be easily molded and reshaped without losing its original properties. Unlike traditional silicone, LSR is injected into a mold under high pressure, allowing for faster cycle times and more complex products.
The Mechanics Behind Liquid Silicone Injection Molding Machines
Liquid silicone injection molding machines operate through a series of well-coordinated steps:
- Preparation: The process begins with the preparation of liquid silicone that is mixed with curing agents.
- Injection: The prepared silicone is injected into a preheated mold using a screw or plunger system.
- Curing: Once injected, the silicone cures in the mold, usually polymerizing at elevated temperatures.
- Cooling: After curing, the mold is cooled, allowing the solidified product to be ejected.
- Finishing: The final product may undergo additional finishing processes, such as trimming and surface treatment.
Advantages of Liquid Silicone Injection Molding Machines
Investing in liquid silicone injection molding technology brings numerous advantages:
- High Precision: These machines produce components with exceptionally tight tolerances, essential for critical applications in electronics and medical devices.
- Rapid Production: The injection molding process is efficient and significantly reduces cycle times, enabling faster turnaround for product launches.
- Material Versatility: Liquid silicone rubber can be formulated to meet a variety of performance requirements, including flexibility, durability, and resistance to extreme temperatures.
- Reduced Waste: The consistency of the injection molding process minimizes material waste, making it a more sustainable option.
- Enhanced Durability: Products made from LSR can withstand harsh environmental conditions, UV exposure, and fatigue, making them ideal for both outdoor electronics and medical applications.
Applications in Electronics
In the realm of electronics, the demand for high-quality, durable components is relentless. Liquid silicone injection molding machines facilitate the production of various products:
1. Sealing and Gaskets
Liquid silicone is an excellent material for making seals and gaskets that require precision in application, ensuring that devices are moisture and dust-resistant.
2. Flexible Connectors
The flexibility and thermal stability of LSR allow for the manufacturing of connectors that can endure repeated-use scenarios without degrading.
3. Encapsulation of Electronics
Liquid silicone can be used in encapsulating electronic devices, providing protection against moisture and chemicals while ensuring thermal management.
Applications in Medical Supplies
In the medical supplies sector, the role of liquid silicone injection molding machines becomes even more critical:
1. Medical Devices
From catheters to syringes, LSR is utilized in manufacturing medical devices that require biocompatibility and precision. These products meet stringent health and safety standards.
2. Implantable Products
The inherent properties of LSR allow for its use in implantable products that require long-term durability and resistance to bodily fluids, making it a favorite among biomedical engineers.
3. Simplification of Complex Designs
With the capability to create complicated geometries, liquid silicone molding can simplify designs that would otherwise require multiple components, reducing assembly time and costs.
Choosing the Right Liquid Silicone Injection Molding Machine
Selecting the appropriate liquid silicone injection molding machine for your business involves considering several factors:
- Production Volume: Assessing your production needs is critical. High-volume operations will benefit from machines with faster cycle times.
- Complexity of Parts: Evaluate the complexity of the parts you wish to produce; some machines are better suited for intricate designs.
- Material Compatibility: Ensure that the machine can handle the specific types of liquid silicone necessary for your applications.
- Cost and Investment: While quality machines can be expensive, consider the long-term return on investment through savings on labor and materials.
The Future of Liquid Silicone Technology
The future of liquid silicone injection molding machines looks promising, with innovations on the horizon:
Automation and Smart Technology
As industries continue to embrace Industry 4.0, automation will play a crucial role in enhancing the efficiency and adaptability of injection molding processes. Smart machines that utilize AI will optimize production parameters in real-time.
Sustainability Initiatives
With a global push towards sustainability, manufacturers of liquid silicone injection machines are focusing on reducing energy consumption and utilizing recycled materials. The development of eco-friendly LSR formulations will play a key role in this transition.
Customization Capabilities
As markets demand more personalized products, customizing molds and machinery setups will become increasingly important. This flexibility will allow manufacturers to address specific client needs effectively.
Conclusion: Embracing Liquid Silicone Injection Molding Machines
The rise of liquid silicone injection molding machines marks a significant advancement in manufacturing technology, providing businesses in the electronics and medical supplies sectors with avenues for innovation and efficiency. By embracing this technology, companies can enhance their product offerings, increase production speed, and maintain the highest quality standards.
As we move into the future, the potential of liquid silicone injection molding is only beginning to be explored. Businesses like Nolato are at the forefront of this transformation, pushing the boundaries of what is possible in silicone engineering. By leveraging liquid silicone technology, manufacturers can not only meet the current demands of the marketplace but also pave the way for groundbreaking developments in product design and functionality.