Understanding Engine Oil Coolers: Enhancing Diesel Engine Performance
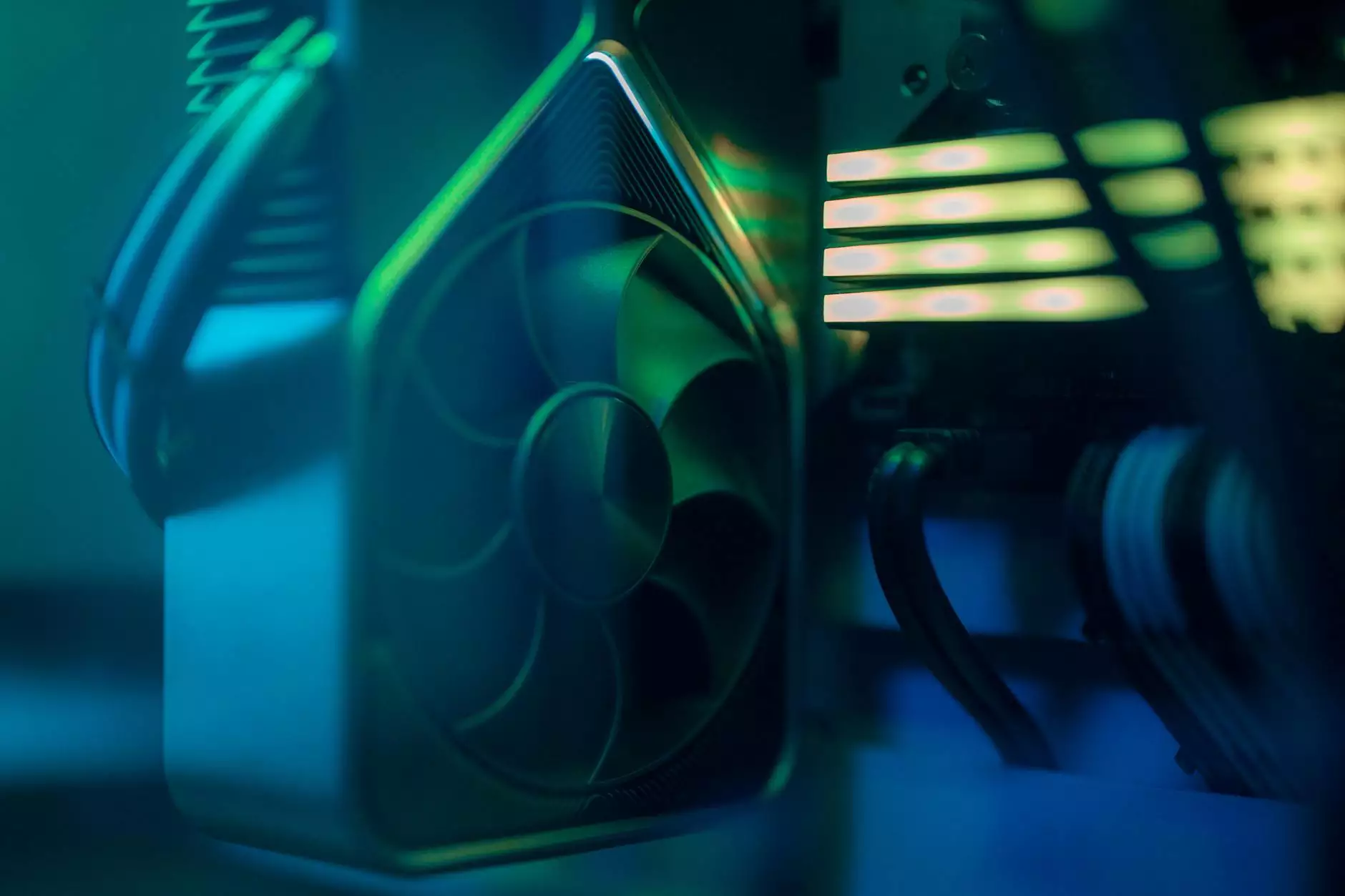
Engine oil coolers play a crucial role in the efficiency and longevity of diesel engines. These components help maintain optimal operating temperatures, ensuring that engines perform at their best under varying conditions. In this article, we will delve into the significance of engine oil coolers, their types, how they function, and the benefits they offer to your diesel engine. Whether you are a diesel engine enthusiast or a professional spare parts supplier, understanding these components will equip you with valuable knowledge to enhance engine performance.
The Significance of Engine Oil Coolers
Engine temperatures can soar during operation, especially in heavy-duty applications typical of diesel engines. High temperatures can lead to premature wear and tear of engine components, increased oil breakdown, and ultimately catastrophic engine failure. This is where engine oil coolers come into play.
By maintaining the engine oil at an optimal temperature, oil coolers improve engine efficiency and protect against overheating. Here are some of the key reasons why these coolers are essential:
- Temperature Regulation: They help manage engine oil temperatures, preventing overheating.
- Improved Engine Efficiency: Cool oil maintains its viscosity better, ensuring adequate lubrication and reducing friction.
- Extended Engine Life: Lower operating temperatures contribute to reduced wear on internal components.
- Enhanced Performance: Engines can achieve optimal performance when operating at the right temperatures, providing better fuel efficiency and power output.
Types of Engine Oil Coolers
There are primarily two types of engine oil coolers: air-cooled and oil-to-water coolers. Understanding the differences between these types can help in selecting the right cooler for your diesel engine.
1. Air-Cooled Engine Oil Coolers
Air-cooled oil coolers use ambient air to dissipate heat from the oil. These coolers are typically mounted at the front of the engine compartment, leading air through fins that extend from the cooler body.
Advantages:
- Simple design and lower cost.
- Lightweight and easier to install.
- Effective in environments with ample airflow.
Disadvantages:
- Less effective in low-speed or stationary conditions.
- Performance highly depends on ambient temperature.
2. Oil-to-Water Engine Oil Coolers
Oil-to-water coolers utilize engine coolant to absorb heat from the oil. Typically, these coolers are integrated into the engine’s cooling system, allowing for more consistent temperature regulation.
Advantages:
- More efficient cooling in varying conditions.
- Less dependency on ambient conditions compared to air coolers.
- Can provide more consistent oil temperatures during operation.
Disadvantages:
- More complex and potentially higher cost.
- Requires careful design to avoid oil contamination.
How Engine Oil Coolers Work
The operation of engine oil coolers can be understood as a two-step process: heat transfer and circulation. Let’s break down how this works in detail:
Heat Transfer
When the engine operates, it generates heat primarily through combustion and mechanical processes. This heat is transferred to the engine oil, which serves to lubricate and protect engine components. A cooler facilitates the disconnecting of heat from the oil, which is crucial for maintaining an efficient engine temperature.
In air-cooled systems, as oil flows through the cooler, it passes through a series of fins that increase surface area. The cooler then allows ambient air to pass over these fins, transferring heat away from the oil. In oil-to-water systems, the oil passes through channels that are in contact with coolant, which absorbs heat and redirects it to the vehicle’s radiator.
Circulation
For optimal efficiency, it is essential for the engine oil to circulate freely through the cooler. Most diesel engines employ a pump that helps to circulate oil to various engine components, including the cooler. This continuous flow ensures the cooler maintains oil temperatures, allowing for high-performance levels.
Benefits of Installing Engine Oil Coolers
Integrating engine oil coolers into diesel engines offers a multitude of benefits. Let’s explore some of the key advantages:
- Prevention of Oil Breakdown: Lower temperatures reduce oxidation and degradation of oil, prolonging oil life.
- Improved Fuel Efficiency: Engines operating at optimum temperatures consume less fuel due to reduced frictional losses.
- Enhanced Performance under Load: Heavy-duty applications benefit significantly from regulated oil temperatures during extended operation.
- Reduced Maintenance Costs: By preventing engine damage and wear, oil coolers contribute to lower long-term maintenance expenses.
Choosing the Right Engine Oil Cooler
Selecting the correct engine oil cooler for your diesel engine is essential to maximize its benefits. Consider the following factors when making your choice:
1. Engine Size and Type
Different engines have varying cooling requirements. Heavy-duty industrial engines may necessitate more robust cooling solutions compared to light-duty applications.
2. Operating Environment
Assess whether the engine is primarily used in hot or cold climates. This knowledge directly affects whether an air-cooled or oil-to-water cooler is more suitable.
3. Installation Space
Understand the available space in your engine compartment. Some coolers may require more room due to their design, affecting installation feasibility.
4. Budget and Cost-Effectiveness
Consider your budget while also evaluating the long-term benefits. Sometimes, spending a bit more on a high-quality cooler can save money on maintenance and repairs in the future.
Common Misconceptions about Engine Oil Coolers
Despite their importance, there are several misconceptions about engine oil coolers that can lead to misunderstandings:
Myth 1: All Engines Need Oil Coolers
While oil coolers are beneficial, not all engines require them. Small engines often have sufficient cooling through natural airflow and do not typically experience the same level of heat generation as larger diesel engines.
Myth 2: Oil Coolers Always Improve Performance
While oil coolers can enhance performance in many cases, they must be appropriately matched to the engine. An incorrectly sized cooler can lead to issues such as inadequate heating of the oil, which can cause problems in colder climates.
Myth 3: Installing an Oil Cooler is Complicated
While installation may seem daunting, many modern oil coolers are designed for straightforward installation, especially with the help of professionals or following the manufacturer's guidelines.
Maintaining Your Engine Oil Cooler
To ensure the continued performance of your engine oil cooler, regular maintenance is crucial. Here are some maintenance tips:
- Regular Inspections: Periodically check for leaks, corrosion, or damage.
- Cleanliness: Ensure that the cooler’s surfaces are clean, especially for air-cooled systems where debris can obstruct airflow.
- Monitor Engine Temperatures: Keep an eye on oil temperature gauges to catch any anomalies early on.
- Fluid Changes: Follow the manufacturer's recommendations for oil changes to prevent buildup of contaminants that can affect cooling efficiency.
Conclusion
In conclusion, engine oil coolers are critical components that contribute significantly to the performance and longevity of diesel engines. Understanding their operation, benefits, and proper maintenance is vital for anyone involved in the diesel engine parts industry, including both professionals and enthusiasts. As you navigate your options for diesel engine service and parts, consider the integral role of engine oil coolers to ensure optimal engine performance.
For high-quality diesel engine parts and reliable spare parts suppliers, visit client-diesel.com. Enhance your engine's performance and invest in the longevity of your diesel machinery through informed choices and quality components.