Die Casting Automotive: A Revolution in Manufacturing
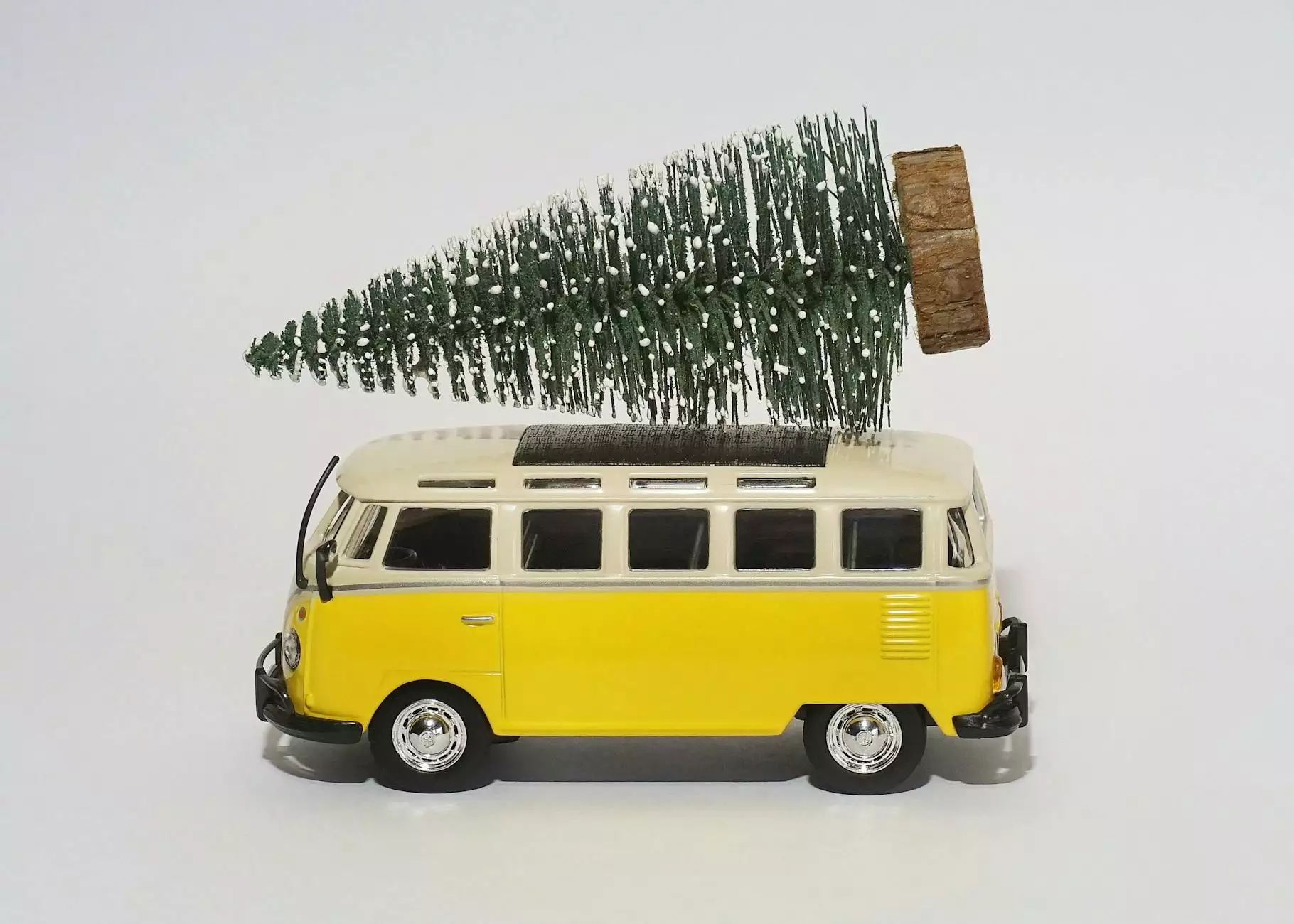
When we think of the automotive industry, innovation and efficiency stand at the forefront. An essential aspect that embodies these qualities is die casting automotive. This manufacturing process has transformed how automotive components are produced, ensuring they are made stronger, lighter, and more efficiently than ever before. In this article, we delve into the intricacies of die casting, its significance in the automotive industry, and how companies like Deep Mould are making strides in this field.
Understanding Die Casting
Die casting is a metal casting process that involves forcing molten metal into a mold cavity under high pressure. This method is particularly advantageous for creating complex shapes with high precision. The process can utilize various types of metals, including aluminum, zinc, and magnesium, with aluminum being the most commonly used in the automotive sector.
How Die Casting Works
The die casting process typically involves several critical steps:
- Preparation: The die is preheated and lubricated to ensure smooth ejection of the finished part.
- Injection: Molten metal is injected into the die using a mechanical or hydraulic press at extremely high pressures, usually between 1,000 to 20,000 psi.
- Cooling: Once the metal fills the die, it is allowed to cool and solidify for a predetermined time.
- Ejection: After solidification, the mold is opened, and the part is ejected.
- Finishing: Additional finishing processes may be applied, such as polishing or machining, to achieve the desired surface quality.
The Benefits of Die Casting in the Automotive Industry
The die casting automotive technique offers numerous benefits that make it an attractive option for manufacturers:
1. Improved Strength-to-Weight Ratio
Automotive components made through die casting are often stronger than those produced using traditional methods. The high-density structure of die-cast metals allows for a superior strength-to-weight ratio, making vehicles lighter and more fuel-efficient.
2. High Precision and Complexity
Die casting enables the creation of intricate designs that are not only aesthetically pleasing but also functionally superior. This is invaluable in the automotive industry where both complexity and precision are required.
3. Cost-Effectiveness
While the initial cost of creating die molds can be significant, the long-term savings in production costs make die casting highly economical. High production volumes can significantly reduce the cost per component.
4. Reduced Waste
Compared to traditional machining methods that often result in considerable material waste, the die casting process uses close to 100% of the metal, thereby reducing waste and lowering costs.
Applications of Die Casting in Automotive Manufacturing
The automotive industry utilizes die-cast components across various applications:
- Engine Components: Cylinder heads, engine blocks, and intake manifolds are commonly produced through die casting due to their complex shapes and the need for high durability.
- Transmission Parts: Die casting is used in creating transmission housings, which require precise engineering to ensure optimal performance.
- Chassis and Frame Components: Components like suspension parts, steering columns, and cross members benefit from the strength and weight savings offered by die casting.
- Exterior Body Components: Grilles, brackets, and other aesthetic components can be manufactured with high detail, contributing to both form and function.
The Future of Die Casting in the Automotive Industry
As the automotive industry evolves toward electrification and sustainability, die casting is expected to play a pivotal role. With the increasing demand for lightweight materials and components, the significance of die casting will likely grow. Here are some future trends to consider:
1. Adoption of New Alloys
Research into advanced die-cast alloys, such as those that combine aluminum with other elements to enhance performance, is on the rise. These innovations will further improve the properties of automotive parts.
2. Integration of 3D Printing
The combination of die casting with 3D printing technologies is beginning to emerge, allowing for more complex mold designs and rapid prototyping, which can lead to faster production times and greater flexibility.
3. Automation and Smart Manufacturing
As the automotive manufacturing landscape embraces Industry 4.0, die casting processes will likely incorporate more automation and IoT technologies, enhancing efficiency and minimizing human error.
Best Practices for Die Casting Automotive Components
To achieve the best results in die casting, companies should consider the following best practices:
- Invest in Quality Molds: High-quality molds ensure better finishes and accurate shapes, reducing the need for post-processing.
- Monitor Process Parameters: Maintaining optimal injection speeds, temperatures, and pressures is crucial for consistent quality.
- Conduct Regular Maintenance: Keeping die casting equipment well-maintained leads to fewer breakdowns and downtime, enhancing productivity.
- Train Personnel: Skilled operators are essential in achieving the precision required in die casting processes.
Conclusion
The importance of die casting in the automotive sector cannot be overstated. As the industry moves toward more efficient and sustainable practices, die casting offers a formidable solution to the increasing demands for performance, weight reduction, and precision manufacturing. Companies like Deep Mould are at the forefront of this revolution, utilizing advanced technologies and skilled craftsmanship to deliver high-quality die casting solutions. Embracing this method not only enhances the capabilities of automotive manufacturers but also contributes to a greener and more innovative future in transportation.