The Rise of Electric Injection Machines in Metal Fabrication
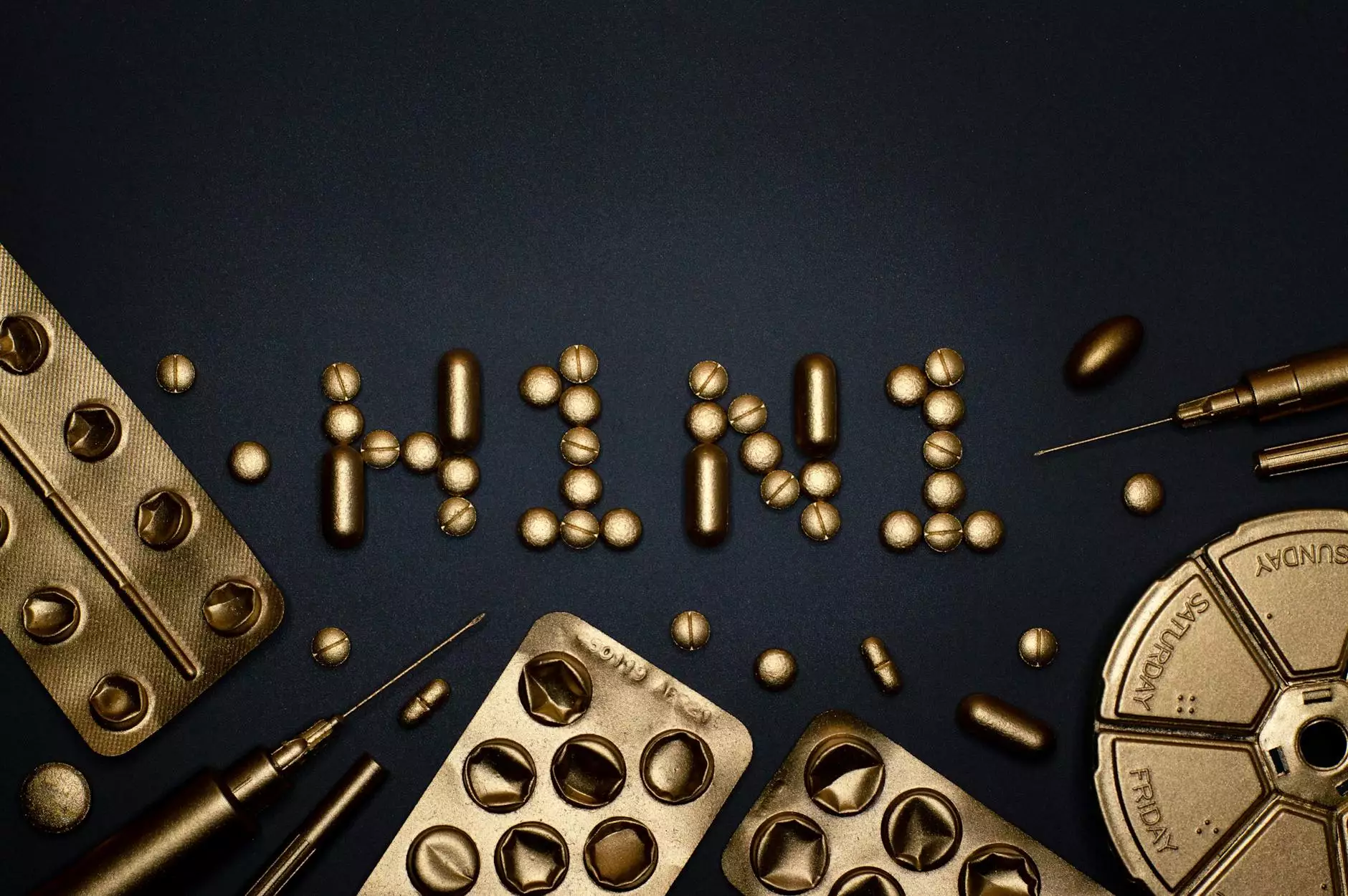
The electric injection machine has emerged as a vital tool in the realm of metal fabrication, transforming how businesses approach production and efficiency. As industries strive for greater precision and speed, the adoption of electric injection machines is becoming increasingly prevalent. This article delves into the features, benefits, and applications of electric injection machines, specifically in the metal fabricators sector, while also exploring how they compare to traditional models.
Understanding Electric Injection Machines
Electric injection machines operate on the principle of electrically driven mechanisms to inject molten plastic or metal into molds. Using electric servo motors, these machines offer precise control over injection speed, pressure, and volume, resulting in superior product quality. Unlike their hydraulic counterparts, electric injection machines are designed with sustainability and efficiency at their core, which is a critical factor in today's manufacturing landscape.
Key Features of Electric Injection Machines
- Energy Efficiency: These machines consume less power compared to hydraulic systems, thanks to their servo-motor technology.
- Precision Control: Electric injection machines provide exact measurements and control, leading to improved product consistency.
- Quieter Operation: They operate more quietly than hydraulic machines, reducing noise pollution in manufacturing environments.
- Compact Design: Electric machines usually feature a smaller footprint, allowing for more efficient use of factory floor space.
- Reduced Maintenance: With fewer moving parts compared to hydraulic systems, electric injection machines require less maintenance, lowering operational costs.
Benefits of Electric Injection Machines for Metal Fabricators
For businesses engaged in metal fabrication, transitioning to electric injection machines brings a multitude of benefits that can significantly enhance operational efficiency and product quality.
1. Increased Productivity
The speed of production is highly critical in the competitive landscape of metal fabrication. Electric injection machines can achieve faster cycle times due to their rapid heating and cooling capabilities, allowing for shorter wait times between production runs. This increased productivity can lead to higher output without compromising quality.
2. Consistent Quality
With precise control over process variables, electric injection machines ensure that each item produced meets the defined specifications. This consistency reduces waste and minimizes rework, ultimately saving on costs. Furthermore, the ability to maintain temperature control leads to fewer defects during the manufacturing process.
3. Lower Operating Costs
Investing in electric injection machines means lower utility bills due to their energy-efficient design. The reduction in maintenance costs, coupled with fewer defects and rework, contributes to a more economical operation, allowing businesses to invest savings into other areas of growth.
4. Environmentally Friendly Practices
With a growing emphasis on sustainability, electric injection machines align perfectly with eco-friendly manufacturing goals. They produce less waste through precise manufacturing processes and consume less energy, contributing to a lower carbon footprint.
Applications of Electric Injection Machines in Metal Fabrication
Electric injection machines find applications across various sectors of the metal fabrication industry, enhancing capabilities in numerous ways.
1. Automotive Industry
In the automotive sector, electric injection machines are utilized for producing intricate parts with high precision. Components such as housings, connectors, and other electrical components benefit from the accuracy provided by electric systems.
2. Aerospace and Defense
The aerospace industry demands the highest levels of quality and precision. Electric injection machines allow for the manufacturing of lightweight and durable components, crucial for enhancing aircraft performance and safety.
3. Consumer Electronics
With the rising complexity in consumer electronics, electric injection machines enable manufacturers to create parts with intricate designs, ensuring they remain competitive in the market.
4. Medical Devices
Electronics play a key role in the manufacture of medical devices. The need for precision and compliance with stringent regulatory standards make electric injection machines an ideal fit for this industry, facilitating the production of high-quality, safe, and reliable medical components.
Comparing Electric and Hydraulic Injection Machines
When considering the shift to electric injection machines, it is essential to understand the differences between electric and hydraulic models.
Efficiency and Cost
Hydraulic machines tend to have higher operating costs, primarily due to their energy consumption and need for frequent maintenance. Electric injection machines, on the other hand, offer significant savings over time as they consume less power and require less frequent service.
Precision and Control
Electric machines provide superior control over the injection process, resulting in higher precision and speed. This advantage is particularly beneficial when manufacturing complex parts that require strict adherence to specifications.
Environmental Impact
With the increasing focus on sustainability, electric injection machines play a crucial role in reducing energy consumption and manufacturing waste. Their environmentally friendly design makes them a preferred choice for companies aiming to implement green practices.
Investing in Electric Injection Machines: Strategic Considerations
Before making a significant investment in electric injection machines, businesses should evaluate several strategic factors to ensure the transition effectively meets operational goals.
1. Analyzing Production Needs
Assessing current and future production requirements is essential. A thorough analysis helps determine the appropriate size and specifications of electric injection machines necessary to meet demand.
2. Understanding the Market Landscape
It's critical to stay informed about market trends and competitive practices within the metal fabrication industry. By understanding what competitors are doing, businesses can leverage electric injection machines to gain a competitive edge.
3. Training and Development
Proper training for staff on the operation and maintenance of electric injection machines is necessary for maximizing their benefits. Organizations should invest in training programs to ensure a smooth transition and effective operation.
The Future of Electric Injection Machines
As technology continues to advance, electric injection machines are expected to become even more sophisticated. Future developments may include enhanced automation, artificial intelligence integration for improved process efficiency, and even greater energy efficiency. As the demand for high-quality, precision-produced components increases, the electric injection machine will undoubtedly play a vital role in shaping the future of manufacturing.
Conclusion
In conclusion, the benefits of shifting to an electric injection machine in the realm of metal fabrication are undeniable. From increased productivity and reduced costs to a commitment to sustainable manufacturing practices, electric injection machines are paving the way for the future of manufacturing. For businesses looking to enhance their operations, embracing this technology is not just an option—it’s a strategic necessity.
Explore Electric Injection Machines at DeepMould
At DeepMould, we provide leading-edge solutions in electric injection machine technology tailored for metal fabricators. Our commitment to quality and innovation positions us as a prominent player in the industry, and we invite you to learn more about our offerings and how we can contribute to your manufacturing success.